This all-of-the-above project involved electrical system design, industrial automation design and installation, PLC programming, and installation of industrial control panels and motor control equipment. The design phase incorporated calculating the electrical load for all equipment, lighting, outlets, etc within the building, calculating the size of the electrical service, feeder cables, conductor and conduit sizes, and then designing panel locations, lighting layout, outlet and switch locations. This was all drawn into a full sized set of blueprints that were provided for construction. After the construction was complete, the automation and control system was designed to provide full automation of the entire process. Industrial control panels were built for each individual piece of equipment, Variable Frequency Drives (VFD’s) and Soft Starters were installed and programmed. One centralized PLC cabinet using a Schneider Modicon PLC along with a mobile HMI station, provided the control and monitoring of the entire factory. The mobile HMI station was designed so that it can be moved to anywhere in the facility giving the operator the ability to physically view any stage of the process while having full supervisory control and data analysis (SCADA) of the entire process. The Human Machine Interface (HMI) has the ability to display how much material is being processed by certain pieces of equipment. It also provides real-time speed controls where the operator can adjust the speed of each conveyor to speed up or slow down the material moving.
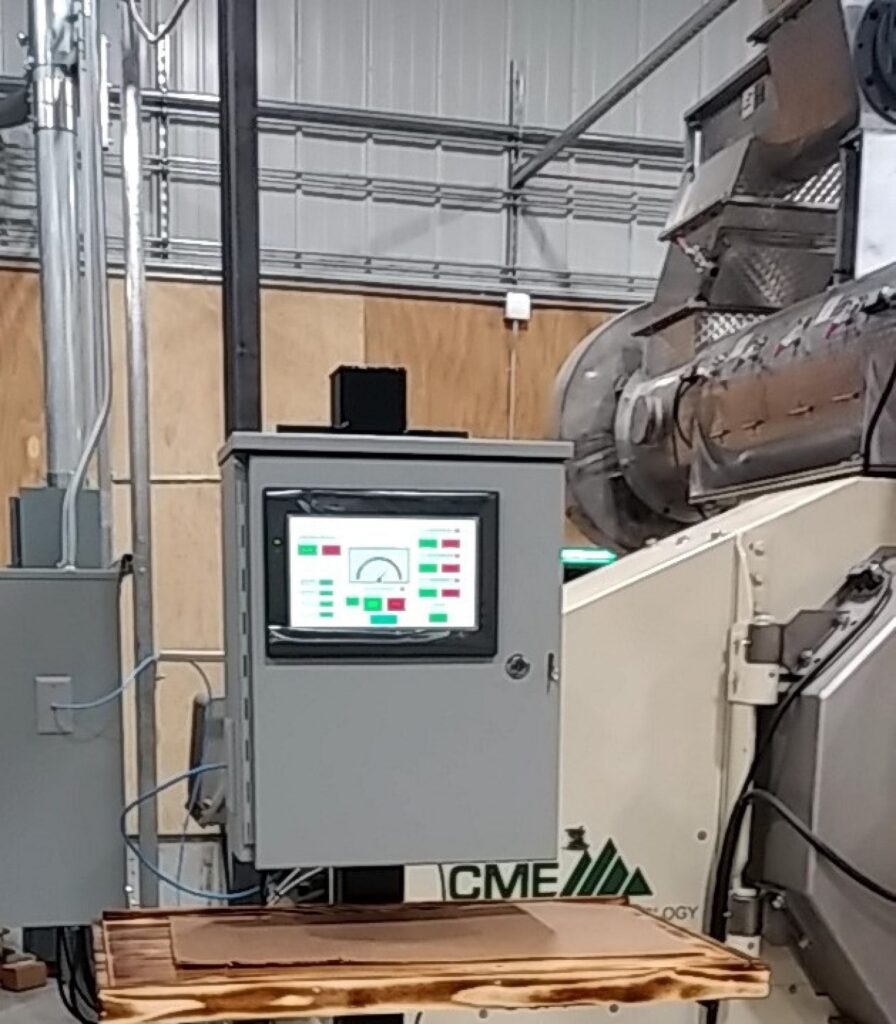
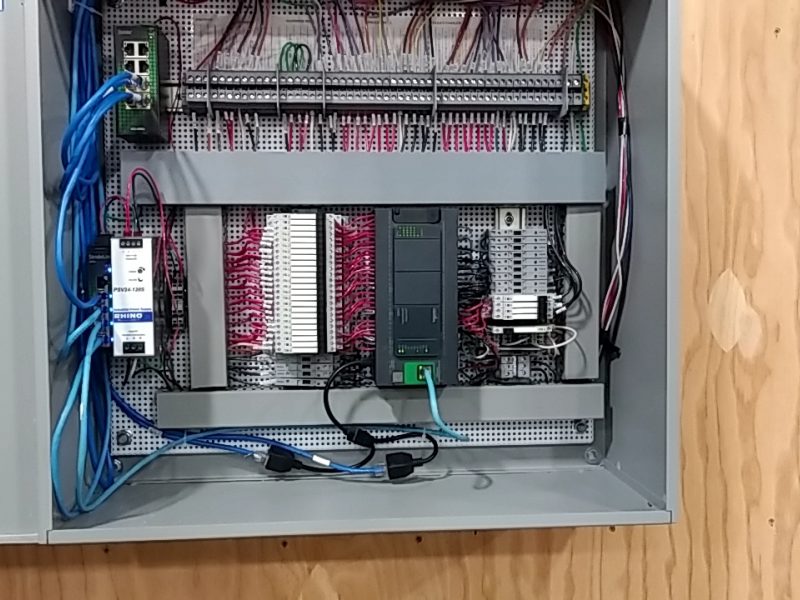
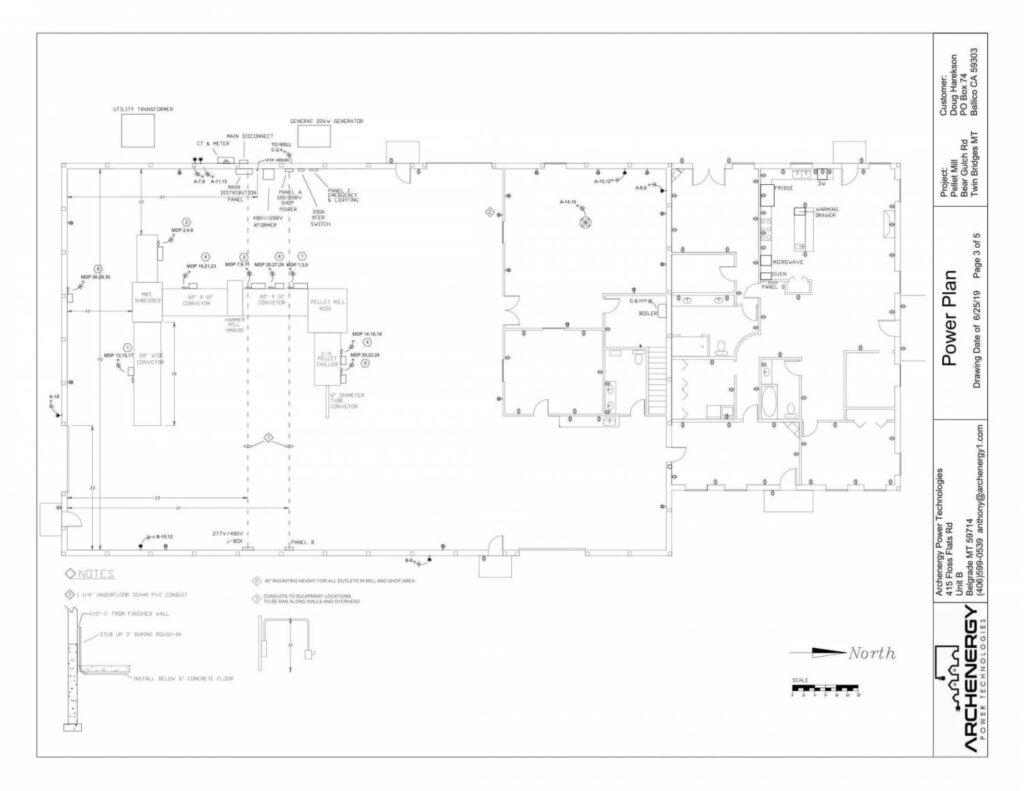
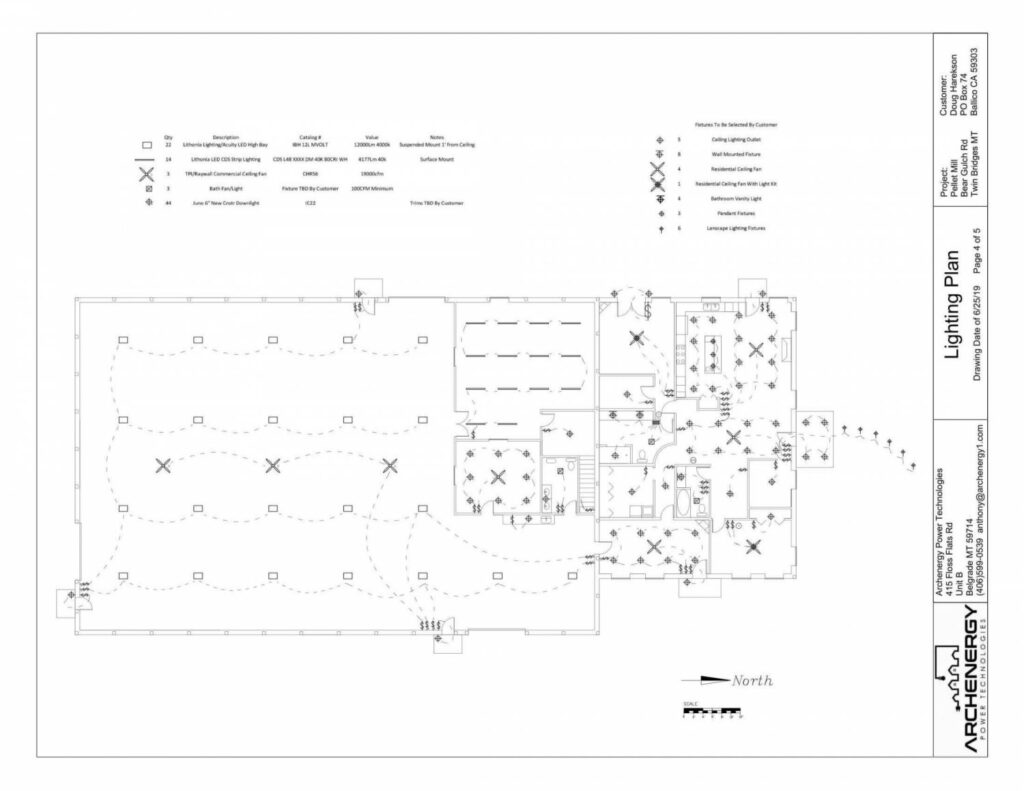